Service Air Suspension System Immediately error appears due to problems like electrical shorts, air leaks, faulty ride height sensors, aging components, moisture damage, software bugs, and environmental factors that disrupt the air suspension system’s operation.
Diagnosing the root cause for Service Air Suspension System Immediately issue requires methodically testing each component using visual inspections, computer scans, pressure tests, voltage checks, bounce assessments, and parts replacements. Addressing any mechanical or electrical defects promptly through troubleshooting and repairs will restore system functionality and reliable performance.
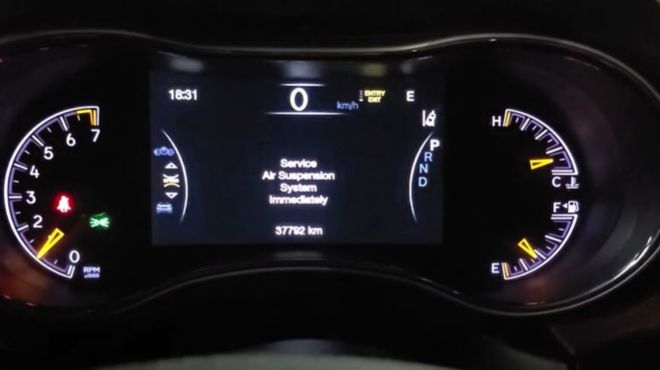
In this post, I’ll walk you through all the typical issues that could trigger that message and equip you with fixes to get your Jeep suspension rolling again.
What Causes the Warning Message?
Weak 12V Battery
A lot of times, that scary service message is set off by something simple – a worn out 12-volt battery. Just like when the battery dies in your cell phone after a few years, the battery providing power to your Jeep can start to run down after extended use. This can cause some flaky electrical behavior that makes your Jeep’s computer freak out unnecessarily about the air suspension.
Before panic sets in, have your battery tested to see if it’s operating at lower capacity. Replace it with a fresh new battery and the warning light may be gone just like that! Easy fix.
Leaking or Damaged Air Springs
If your battery checks out fine, the next thing to examine is those all-important air springs or “air struts” as we mechanics call them. See, just like tires can get nails or leaks, the air suspension bags that cushion your ride can become punctured or develop small cracks over time.
Listen closely after parking your Jeep – do you hear air hissing out anywhere around the wheels and suspension? That’s the tell-tale clue of a leak in one of the air bags. Have a pro mechanic inspect each one and replace any that are compromised. That should get your air supply restored and turn off the warning light.
Air Compressor Failure
Another important component to a well-functioning air suspension system is the air compressor. This is essentially a compact electric air pump that maintains the right amount of air pressure in those suspension bags at all times.
If your Jeep’s air pump stops being able to top up the air bags for some reason, it can again set off that dreaded warning light situation. Reasons the air compressor may fail include:
- The pump motor wearing out over time
- Electrical connection issues
- Stuck or damaged pump valves
- Debris getting lodged in the mechanism
A trained mechanic can diagnose if the compressor is no longer able to build enough air pressure by using a gauge and testing its performance at filling the system. Replacing the air pump assembly may be required to get you smoothly gliding atop your shocks again.
Faulty Sensors
There’s also a bunch of position and pressure sensors scattered around the air suspension framework that help monitor what’s going on. Like nerves sending signals back to the brain. If these sensors get damaged by road debris or develop internal electrical issues, they can send wacky false signals to the computer. Garbage in, garage out, as they say!
A mechanic can troubleshoot this by watching the sensor readings fluctuate oddly while the vehicle is operating. Heading down the highway, are the ride height sensors jittering all over the place? Replace the wacky one! Diagnosing sensor glitches just takes time and an understanding of how they’re supposed to work.
Wiring or electrical issues
So you’ve checked all the mechanical parts of the air suspension system, but the pesky warning light refuses to turn off. Time to dig deeper into the electrical side of things!
Like many aspects in modern cars, the air suspension relies on complicated wiring and modules to operate properly. Problems can happen when:
- Wire insulation becomes cracked or wires are chewed by rodents (hey, it happens!)
- Corrosion causes connectivity issues in electrical connectors
- Fuses and relays related to the system burn out
- The suspension control module just decides to be cranky
Diagnosing tricky electrical gremlins takes some patience, I won’t lie. Checking each wire and component one at a time. Wiggling this, tapping on that with a wrench. Ugh!
But an experienced mechanic has all sorts of arcane tricks up his/her sleeve for smoke-testing wires, resetting hidden control units you didn’t know you had, and generally coaxing your air suspension’s electrical bits back to proper operation. Consider it magical mechanic voodoo – don’t try this without years of experience!
If we’ve struck out on every other potential culprit, it’s time to dig out the wiring diagrams and start the long yet rewarding journey of unclogging your Jeep’s electrical arteries. Wire by wire, we’ll get that heart pumping smoothly again!
Control Module Malfunction
In addition to wiring problems, the brain of the air suspension system – the ride control module – can also just outright fail. This computer chip processes data from all the sensors and makes adjustments to things like ride height. After years of service, they degrade over time or get damaged by electrical spikes.
Diagnosing a faulty control module requires plugging into its data port and looking for clues like inconsistent readings that don’t match the sensor inputs. Alternatively, a replacement module can be swapped in to rule out the old one being bad. While not a cheap fix, installing an updated replacement module often solves persistent air suspension issues.
Excessive Vehicle Weight
Here’s a common mistake – consistently overloading your Jeep with passengers and cargo beyond the factory ratings. All that extra weight pressing down flexes the suspension components more than intended. Air springs and dampers wear out faster. The compressor strains to maintain pressure levels. Warning lights angry!
While the air suspension system is built to handle some heavy loads, don’t push it beyond the recommended Gross Vehicle Weight Rating capacity on a regular basis. You risk accelerated wear and those dreaded warning messages. Give your Jeep a break by removing heavy junk in the trunk or letting some friends ride in another car once in a while.
Moisture and Corrosion
This one may surprise some folks. Something as small as a clogged drain hole or cracked weather seal can eventually lead to electrical gremlins and air suspension errors. See, moisture and road grime has a way of getting everywhere over time. It slowly corrodes connectors and builds up mineral deposits. Sneaky!
Pay attention for damp carpets, mud packed into frame rails, or corrosion on electrical components near the air springs. Carefully cleaning drains holes and fixing any water leaks goes a long way. Spray some anti-corrosive lubricant on electrical connectors if they have surface rust. And consider getting the undercarriage washed more often to prevent crud buildup near suspension parts. Take care of wetness issues promptly to avoid annoying sensor and electrical headaches!
Rubbing Air Lines
You may not realize those critical air hoses and nylon lines routing air throughout the suspension move around quite a bit as you drive. Over many miles, some lines can sag and make rubbing contact with suspension or chassis components. This can wear through the protective outer layer and cause eventual air leaks.
Pay attention for signs of air line rubbing – inspect them closely for wear spots, listen for soft squeaking noises from undercarriage over bumps, etc. Any damaged air hoses or tubes should be replaced. And you can also have aftermarket suspension lift kits installed that relocate the air lines further away from hot exhaust or suspension parts. Preventing line rub saves headaches!
Extended Inactivity
Don’t just let your Jeep sit unused for months on end if you can help it. All sorts of mysterious gremlins like to creep up when cars sit neglected for too long. Rubber dries up, sensors get wonky, moisture builds up in weird places. You see where I’m going with this…
The air suspension system hates extended downtime. Air springs can develop micro-leaks from drying out. Internal electric pump parts seize up from gunk. If your lifestyle keeps the Jeep parked for over a month at a time, take some precautions. Consider occasionally starting it and letting the air pump cycle, inspecting under the hood for critter nests after storage, covering intake openings so mice don’t sneak in, etc. Stay vigilant against inactivity gremlins!
Leaking Quadra-Lift Suspension
Own the Trailhawk or Summit model with full Quadra-Lift air suspension? Congrats, now you have twice the components to worry about! The fancy Quadra-Lift system controls ride height in each corner separately. With great power comes great…leaks.
Quadra-Lift isolator valves are notorious for allowing small air leaks between corners after years of cycling. Have your dealer inspect the system closely for leaks if ride height behaves oddly side-to-side. Resealing leaky Quadra-Lift bits restores proper functionality and gets rid of suspension errors. Fancy trucks need extra fancy servicing!
Cold Weather Issues
Last but not least, never underestimate how cranky mechanical components get in extreme cold weather. Rubber air lines and seals stiffen up. Metal contracts. Pressures fluctuate. No bueno for air suspensions, especially higher-end Quadra-Lift systems.
Below -20°F, faults can randomly pop up as components get “cranky.” Don’t panic, a good blast of heat from the mechanics shop thaws things out. Consider an insulated garage if parking outside in harsh winters. Let her warmup sufficiently before hitting the frozen tundra. With care taken against the cold, your Quadra-Lift Jeep will impress all those diversity bros!
Also see – Service Electronic Throttle Control Jeep Warning: How to Fix?
Steps to Fix the Air Suspension Problems
Alright, we’ve gone through all the usual suspects that can cause air suspension faults. Now comes the fun part – tackling those pesky issues to stop the errors dead in their tracks! Here’s a few first steps to try:
Perform a Bounce Test
Sometimes going back to basics reveals useful clues. Find an empty parking lot and drive at moderate speeds over some speed bumps. Listen and feel how the suspension rebounds after compressions. Hear any odd clunks or leaking noises? Do certain corners feel bouncier or stiffer than others? Does it ride level after testing all four corners? Gather key sensory intel to help narrow down issues. Low-tech but effective!
Reset Air Suspension System
Before cracking open the toolbox, try the old “turn it off and on again” trick. Use the instrument cluster controls to completely deflate then re-inflate the air suspension (carefully in a garage of course). Or disconnect the battery for 30 mins to reset everything. Then take it for a test drive to see if the warning light behaved. Clearing codes gives the computers a fresh start to hopefully make errors go away.
Use Obd Scanner for Diagnostics
Alright, time to interrogate the brains of your Jeep! A mechanic-grade OBD2 scanner tool can tap into error codes and data from different modules to aid troubleshooting. Does the ride control module show faults for certain sensors or pressure readings? See how values change while driving. Scanner tools provide critical clues to hone in on misbehaving components without guessing. We’ll scanner ‘til we get answers!
Test and Potentially Replace the Battery
As discussed earlier, a worn out 12V battery that can no longer maintain proper voltage to components is a common culprit for electrical gremlins. Use a digital multimeter to test battery voltage. Check while idling, while on accessory power, and during starting to simulate real-world demands.
Does voltage dip excessively or fail to hold a charge overnight? Splurge for a new battery with higher cold cranking amps capacity from your dealership. Reconnect everything, clear codes, and test for proper voltage at ride control module/compressor now. A healthy battery minimizes quirky electrical behavior!
Replace Damaged Air Springs & Struts
Rubber air springs naturally degrade and deflate with too many miles. However, also check your air struts (metal shock absorber housings) for oil leaks or cracks that impact performance. Use a paint pen to mark air lines and monitor if pressures change overnight. What leaks faster – air, oil or both? Any uneven ride heights hint at bad struts too.
Be prepared to pony up for replacement air spring assemblies and/or complete strut units. Luckily factory parts are common and affordable. Slap the new hardware on, holding alignment settings as best as possible. Road test to validate smooth, even ride quality and height now. Like new again!
Replace Air Valve
Pay special attention for leaks at air valve stems during inspections. Similar to tires, cracking or loose valve stem cores on the suspension let precious air escape. Quickly isolate which valve is the problem child by spraying soapy bubble solution while inflating/deflating. Catch that sneaky leak in the act!
Pro tip – keep emergency valve stem cores in your glovebox to practice speedy trailside repairs. Pop on a new valve core, hit it with some sealant for good luck, and be back bombing trails in minutes flat. Valve leaks are annoying but easily bested in a pinch. Jeep folks aren’t quitters!
Replace the Air Compressor
The hardworking air compressor pump is another common failure point. Warning signs include slow inflation times, inability to reach target pressures, or seized motor. Tap into the air lines during operation to check if ample air volume is coming out. Assuming the control wiring checks out, compressor problems usually call for a rebuild or replacement.
Many shops can economically rebuild your compressor motor and valves if accessible, breathing new life once again. If not, OEM Jeep and quality aftermarket replacement air compressors are plentiful. The replacement job isn’t too painful if you have some wrench skills and wiring know-how. Those wheels will happily roll on air in no time!
Replace Faulty Sensors
If scanner data shows a position sensor, ride height sensor, or pressure sensor bouncing around erratically, it likely needs replacement. Troubleshoot wiring first, but flaky sensors mean their internal components are failing. Time for fresh hardware.
Locate the series of sensors mounted along the air suspension hardware during installation. Unclip the old sensor, disconnect the wiring harness, then plug in the new replacement part matching form and function. Clear codes and calibrate if needed via scanner tool so the computer relearns healthy readings. Happy sensor, happy life!
Inspect and Repair Electrical Wiring Issues
Over many miles, air suspension wiring harnesses can degrade from vibration, moisture, and debris ingress. Inspect along the entire wire path looking for common issues:
- Chafed or rubbed through insulation
- Corroded or loose connectors
- Melted wires near hot components
- Rodent nibbling damage (Hey, nature happens!)
Carefully repair wires with electrical tape/splice connectors as able. Spray down corrosion, secure connections. Replace entire wire segments if unsalvageable. Verify handy fuses and relays are intact too. Restore those electrical nervous system pathways one stretch at a time until your air suspension’s electrical woes are history!
Attempt Control Module Repairs or Replacement
The brains of the operation – the ride control module – can cause all sorts of problems if it becomes damaged or corrupt. Attempt resetting and reflashing the module using the dealer’s diagnostic tools to restore proper software operation. If that fails, replacement time.
Swap in a new module matched to your Jeep’s specs using wiring diagrams. Program the latest firmware from scratch. With teaching and calibration, the fresh module should have your air suspension floating on air once again!
Stop Overloading Your Jeep
Ya gotta show your long-suffering vehicle some mercy! Overstuffing your Jeep constantly with heavy cargo and passengers taxes the suspension components quickly. Lighten the load to OEM-recommended limits before problems spiral out of control. Spread gear over multiple trips or take the roof storage pod instead sometimes. Let those air springs decompress!
While you’re removing junk, now is the perfect time to inspect everything under the hood and chassis when it’s not weighed down. Check for binding, leaks, uneven ride height and other issues to address. Heavier doesn’t always mean happier!
Clean All Corrosion and Moisture
We mentioned earlier how trapped moisture and road grim leads to corrosion issues over time. Use a flashlight to poke around the chassis and electrical connectors near air suspension hardware. Look for green fuzzy oxidation, white mineralization stains, or dampness where it shouldn’t be.
Carefully clean any surface deposits, spray down corrosion inhibitor chemicals, and seal up errant water intrusion paths. Prevent further moisture contamination at all costs. Removing its foothold keeps gremlins at bay for the long run!
Locate and Fix Air Leaks
As discussed earlier, small air leaks in the suspension components can trigger fault codes. Thoroughly inspect air springs, struts, valves, lines, fittings, seals and o-rings yet again for escaping air. Use soapy water solution to bubble test while system is pressurized if unsure. Determine root cause of leaks (cracks, loose fittings, etc).
Repair or replace any leaky pieces with new properly sealing versions. Re-assemble carefully to avoid new leaks. Clear codes and verify ride height holds steadily overnight without sinking. No more stray hissing sounds means victory over stubborn air leaks at last!
Drive Regularly to Avoid Inactivity Issues
If your Jeep often sits unused for weeks on end, problems percolate. Get it warmed up and moving a few miles at least once a week. This circulates fluids, charges the battery, cleans crud from exhaust/intake pathways, and makes the suspension components happy.
Pro Tip: Leave air suspension activated while parked to maintain pressurization, preventing leaks during downtime. And stash some humidity-absorbing packs in the cabin to fight moisture while napping if needed. Don’t forsake your Jeep!
Fix Quadra-lift Leaks
Got the fancy load-leveling Quadra-Lift system? Four corners of air bladders means four times the potential for leaks! Inspect isolator valves closely for escaping air side to side. Update leaky seals and o-rings to restore it to working order. Extra TLC required to keep your glitzy suspension in top shape!
Take Cold Weather Precautions
Lastly, cold weather below 20°F can make rubber lines and seals sluggish on all air suspension systems. Install heat deflectors, keep her garage parked on icy nights, let the engine warm fully before hitting snowy roads. Come spring, give everything a thorough de-icing, clean and lube. With prep, your Jeep laughs at old man winter’s fury!
Let’s Wrap This Up
Alright folks, that sums up the common causes and repair fixes needed when the “Service Air Suspension” warning alarm triggers seemingly out of nowhere. While various gremlins can strike, a methodical walk-through of each system component helps narrow down issues quickly.
Don’t panic when you see the message first appear. But also don’t neglect it for too long! Address any underlying problems promptly to prevent bigger headaches. And consider periodic maintenance like fluid changes, minor seal replacements, inspections, and tune ups that extend the healthy years of service life.
With newfound knowledge to tame your Jeep’s air suspension woes, smile confidently as you float off into the sunset. Happy and hassle-free adventures await!